Впервые заводы могут интеллектуально сопоставлять данные о качестве колец и данные о качестве намотки в единой системе, что значительно повышает рентабельность. RSO 3D — это «третье измерение» качества. Пример из практики показывает, как фабрика добилась реальной прибыли, с жизненно важными цифрами, подтверждающими это.

Отображение качества отдельных веретен
Амбициозный прядильщик стремился выйти на новый уровень управления качеством. Для этого клиента было важно, чтобы качество, а также рентабельность должны были быть улучшены. На средней прядильной фабрике в Индии в рамках проекта расширения была установлена система Uster-Muratec RSO 3D. Установка включает 30 компактных кольцепрядильных машин с Uster Sentinel в сочетании с Muratec QPRO EX / FPRO EX с очистителями Spin Inspector и Uster Quantum. На этих машинах заказчик производит 100% гребенную хлопчатобумажную пряжу марок Ne 26 и Ne 32.
Преимущества в процентах
При запуске новой установки было выполнено прямое сравнение между RSO 3D и стандартной установкой в качестве пробы, чтобы продемонстрировать разницу.
Доказательства показали, что прядильщику удалось сократить количество дефектов пряжи на 10 % и количество аварийных сигналов пряжи на 12 % в обоих подсчетах с помощью RSO 3D. Качественные блоки были сокращены еще на 7% и, наконец, более четкие качественные сокращения на 8%.
В целом, эта прядильная машина смогла сократить общее количество стыков пряжи на 5%, производя примерно на 5 кг хорошей пряжи больше на машину в месяц.
Деньги говорят, ясно
Результаты завода впечатляют. Небольшие расчеты превращают факты в числа. Начнем с энергосбережения. Благодаря уменьшению количества соединений пряжи на мотальных машинах заказчику требовалось меньше сжатого воздуха и, следовательно, меньше электроэнергии для компрессорного агрегата машины. Суммарная экономия составляет примерно 954 кВтч на машину в месяц. Из расчета около 0,08 долларов США (6 индийских рупий) за кВтч это составляет 77 долларов США (5 724 индийских рупии) за машину в месяц. С 30 машинами это составляет 27 720 долларов США (почти 2 миллиона индийских рупий) за весь год.
Помимо финансовой экономии, завод также отметил увеличение уровня «хорошего» материала. Сокращение отходов на 5 кг означает, что каждый месяц на каждую машину можно продать на 5 кг больше хорошей пряжи. С 30 машинами это дает на 1800 кг больше пряжи в год. Исходя из цены в 3,77 доллара США (280 кг индийских рупий), это обеспечивает увеличение продаж еще на 6 786 долларов США (500 000 индийских рупий).
Объединяя оба этих расчета, общая прибыль для прядильщика составляет 2,5 миллиона индийских рупий в год, что эквивалентно примерно 35 000 долларов США в год, не считая значительной экономии за счет сокращения более чистых распилов.
Дополнительные преимущества можно ожидать и в последующих процессах. Меньшее количество разрезов означает, что пряжа имеет меньше потенциальных слабых мест, что приводит к меньшему количеству остановок из-за обрывов пряжи. Это позволяет адаптировать последующие скорости процесса, а заказчик также получает выгоду от улучшенного внешнего вида ткани.
Операторы тоже выигрывают…
Рабочая зона для механизаторов может быть значительно увеличена – при этом снижается фактор стресса. Это возможно благодаря тому, что Uster Sentinel на расстоянии уведомляет операторов об отдельных обрывах пряжи. В системе используются сигнальные лампы в головной части машины, в соответствующей секции и в соответствующем прядильном месте. Таким образом, оператор логически направляется к следующему обрыву нити, вместо того, чтобы усердно искать обрывы нити со всех сторон машины.
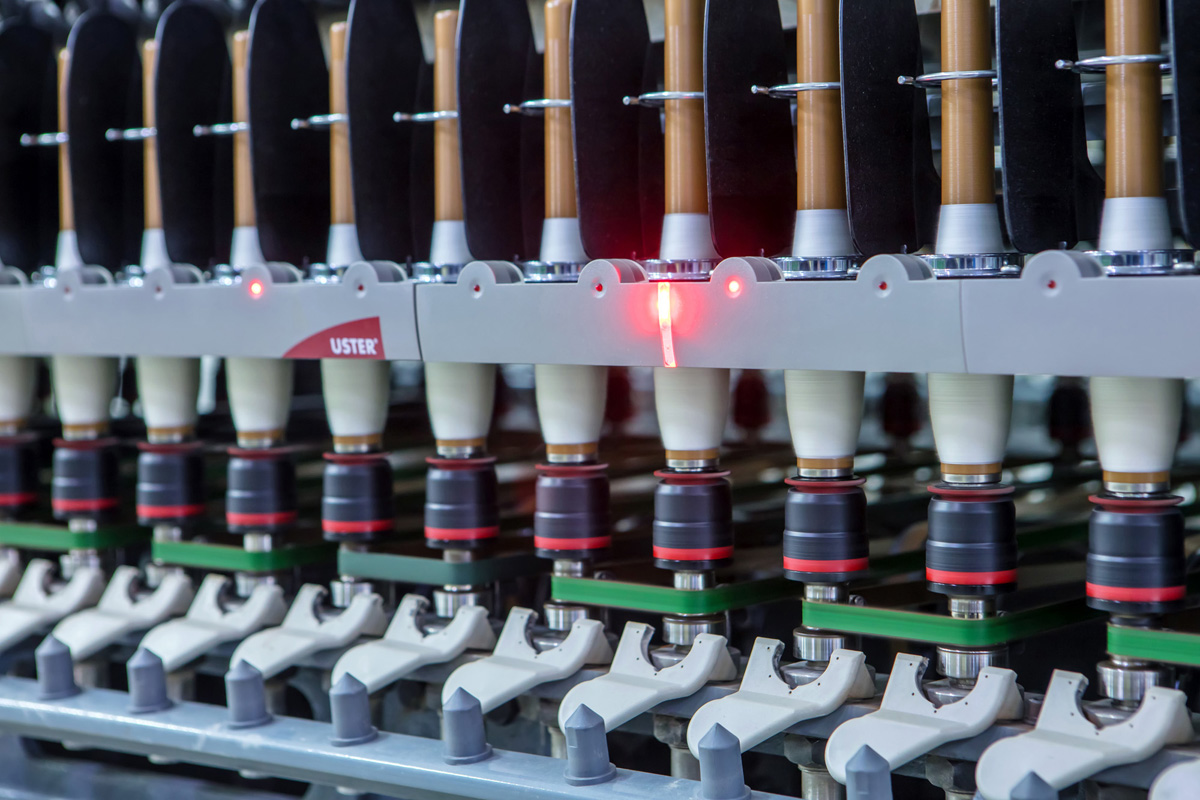
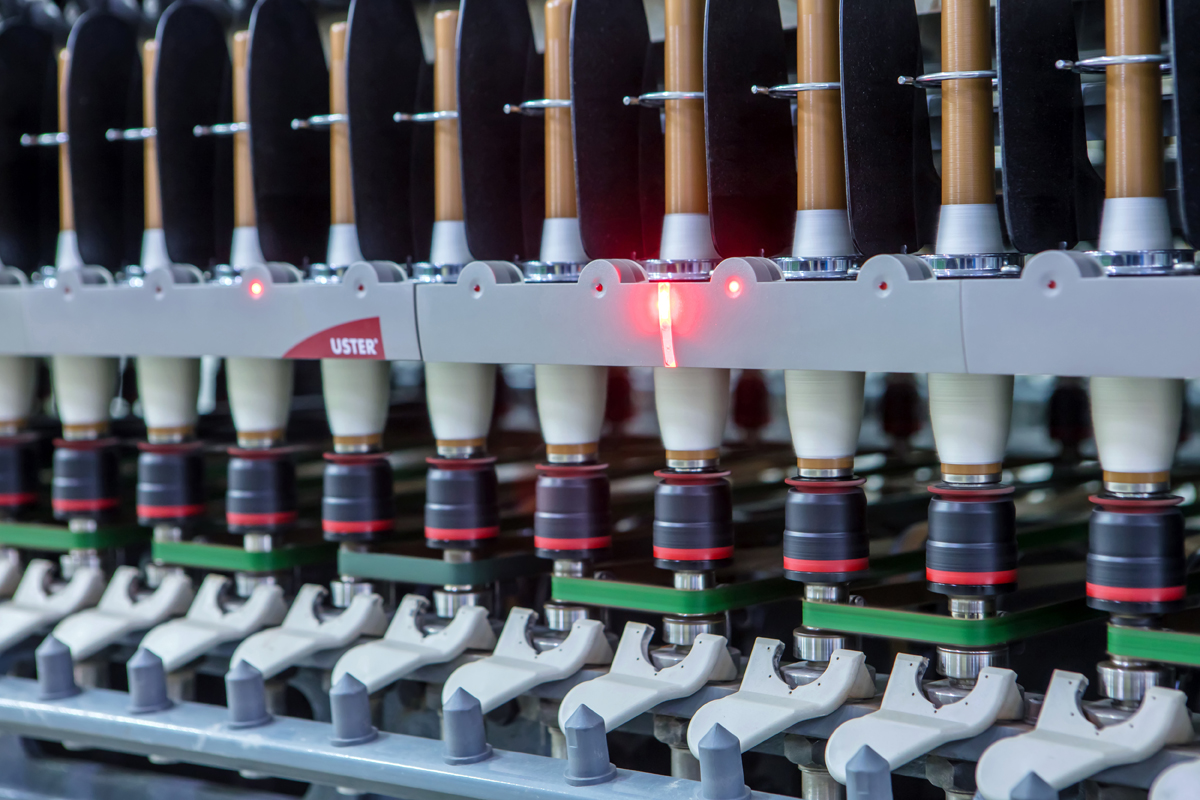
Uster Sentinel установлен на кольцепрядильной машине
Когда оператор обнаруживает обрыв пряжи, тип обрыва указывается на месте прядения. Различные сигналы классифицируют проблему как тревогу Slip, Off Quality, Rogue или RSO 3D. На этой фабрике операторы должны иметь дело исключительно с обрывами пряжи, но не с аварийными сигналами RSO 3D. Это обязанности высококвалифицированных технических специалистов, поскольку сигналы тревоги RSO 3D указывают на неправильную настройку прядильного места, а их устранение необходимо и требует много времени. Аварийные сигналы RSO 3D отображаются для технических специалистов с помощью светодиодов Sentinel, а также на блоке управления Quantum (CCU) и на карте качества RSO 3D.
В результате клиент может развернуть обученный персонал на целевом и эффективном континенте. В то же время фабрика могла увеличить производительность прядения и рабочие зоны операторов за счет оптимизации пути.
Быстрая окупаемость
Индивидуальные данные о качестве для каждой позиции веретена позволяют отображать качество по всей кольцепрядильной машине. Это помогает идентифицировать нестандартные стороны, секции или шпиндели, а также помогает принимать решения по техническому обслуживанию. Картирование качества также позволяет пользователям отслеживать проблемы вплоть до отдельных ровничных машин и катушек. Благодаря качественному картографированию прядильщики могут держать под контролем всю кольцепрядильную машину, а также свою прибыль.
RSO 3D доказывает свою ценность на каждый вложенный цент благодаря экономии средств за счет сокращения использования сжатого воздуха и экономии энергии. Окупаемость наступает раньше благодаря более высокой эффективности производства, основанной на экономии сокращений. Это означает, что дополнительное количество проданной хорошей пряжи равно тому, что в противном случае было бы потрачено впустую на мотальной машине.
«Клиент убежден в Uster RSO 3D из-за повышенной производительности и прибыльности прядения, а также из-за того, что он столкнулся с проблемой нехватки высококвалифицированного персонала за счет использования обученного персонала на целенаправленном и эффективном континенте», — говорит Амол Кекре, генеральный директор. Менеджер по продажам и маркетингу в дочерней компании Uster в Индии.
Более высокая прибыль достигается за счет повышения стандартов качества из-за более плавного хода намотчиков. Претензии остались в прошлом, а повышение эффективности производства гарантировано в будущем. Последующие клиенты прядильной машины также будут рады увеличить скорость производства в своих собственных процессах и в то же время улучшить внешний вид ткани.