Uster Q-Bar 2 becomes the unique formation monitoring system
Uster, Switzerland, 28th April 2021 – The best way to avoid off-quality is simply not to make it. Uster Q-Bar 2 introduces a radical leap in fabric inspection. It monitors the fabric additionally at the earliest point – the critical stage in fabric formation – with automatic, in-line inspection. Identifying problems here brings enormous benefits, preventing defects and enabling weavers to deliver constant quality and stay competitive in the market.
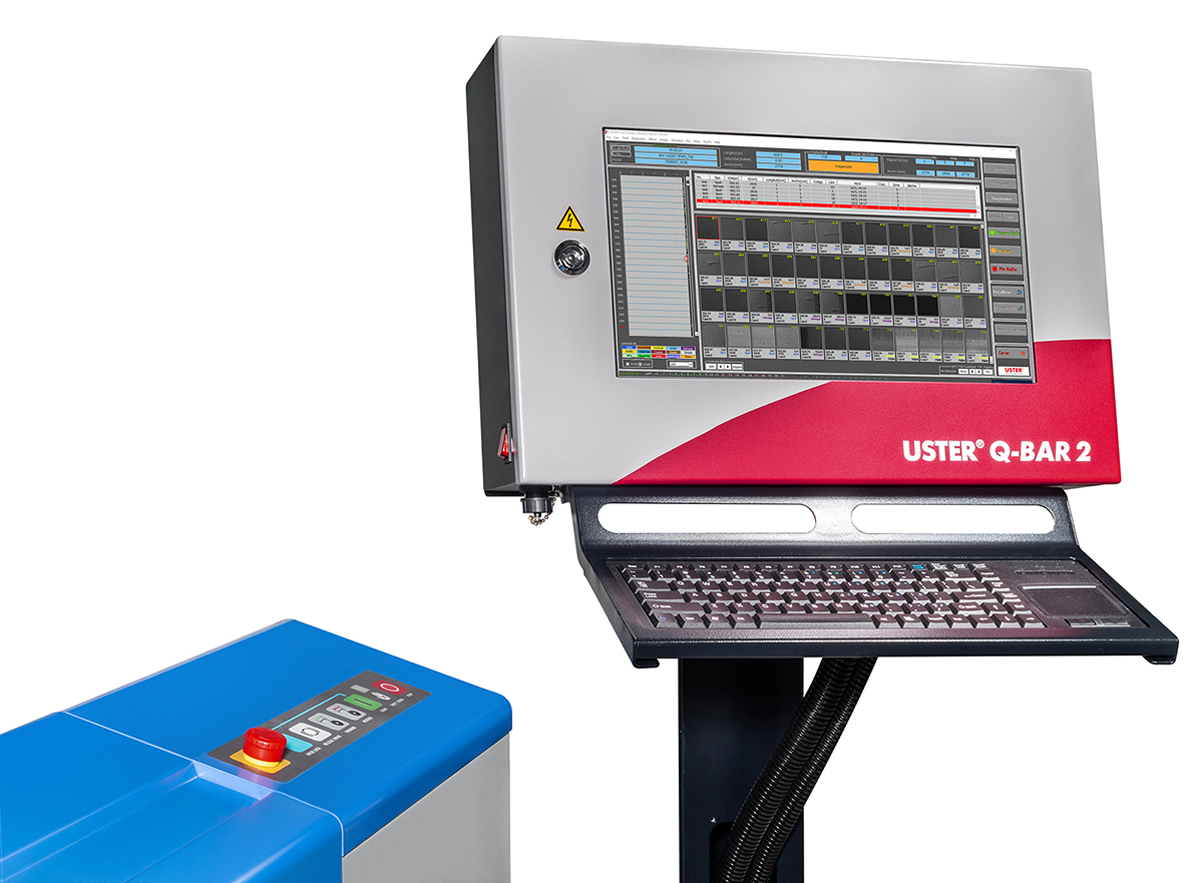
Q-Bar 2 is best described as a formation monitoring system, because of its ingenious positioning directly at the interface of warp and weft threads. That allows rapid response as soon as a defect appears, avoiding long-running or repeating faults. Alarm and stop signals alert the operator to correct problems immediately – and early detection reduces second quality and material loss, as well as minimizing the need for post-production checks.
For weavers, these advantages represent genuine and long-awaited innovations with a positive impact on both productivity and quality.
Formation monitoring
Weaving defects can have various root causes, so Uster Q-Bar 2 provides different algorithms to identify specific defects and their causes. This inbuilt knowledge can prevent defects within the weft insertion cycle.
Its enhanced detection position in the fabric formation zone means the warp is monitored even before it is traversed by the weft – a truly unique benefit. It allows detection of incorrect warp positions, missing warp, loose warp ends and even pattern irregularities.
Another important innovation is the control of weft irregularities. By monitoring each inserted weft in the formation area, Q-Bar 2 primes users to react to weft irregularities at the earliest possible stage. At this point, it can detect weft-related defects such as double picks, broken weft or slubs and loops.
“Formation monitoring is the answer to market requests. Weavers demand zero defect standards, increased sustainability by waste reduction and they want to produce the fabric meeting specific quality requirements,” says Michelle Salg, Product Manager Fabric Inspection at Uster.

Uster Q-Bar 2 – The formation monitoring system
Total supervision
Defects that become visible only in the woven fabric are the nastiest threat. Often, it’s too late when defects such as reed marks, dirty yarns or floats are spotted – but it can’t happen with Uster Q-Bar 2. Its fabric inspection algorithms detect even ‘invisible’ defects in the fabric. It’s the simple solution to improving fabric yield by automated formation monitoring.
Q-Bar 2 also monitors critical machine units in the formation zone. If there is a problem here, the system makes it easy to identify and eliminate it, preventing further defects and again maximizing fabric yield.
Another element of the total supervision provided by the formation monitoring system is its special focus on the selvedge area. This is not only critical for an efficient weaving process, it is also important in further process steps. Specific algorithms detect irregularities in the selvedge, as well as broken leno – but also identify any pattern defects. Continuous pattern monitoring flags up incorrect patterns at the earliest stage, so the loom can be stopped and the problem fixed before many meters of fabric are wasted.
Last but not least, the system has a permanent eye on the fabric width, an essential factor for further processing. For this reason, Q-Bar 2 provides continuous width measurement of the woven fabric, from loom setup to full roll.
Designed for users
The technology in this new formation monitoring system is impressive, but Q-Bar 2 is highly developed in many other aspects too. Its attractive industrial design is also ergonomic, so users have easy access to all important parts. Weavers appreciate its simple installation on existing weaving machines. And operators like the integrated LEDs used by Q-Bar 2: system status is indicated and the positions of detected defects shown by red lights. The improved hardware platform is capable of handling high loom speeds and is ready for future innovations.
First-quality production, to customer specifications, is the overall goal. That is especially important in demanding applications such as industrial and safety textiles. In apparel and home textiles too, it is vital to avoid seconds and minimize waste fabric. “Independent of the fabric application, Uster Q-Bar 2 is a game-changer. For the first time, weavers can actually prevent weaving defects instead of only reacting to them,” says Salg.