Uster, Switzerland, 6th September 2022 – Drylaid nonwovens producers operate to the most stringent quality levels – with zero-tolerance standards for defects bigger than 1 mm. In this nonwovens segment, end-product quality depends absolutely on the efficiency of contamination sorting, early in the process. Uster’s exclusive solution ensures best- possible initial inspection and removal of contamination.
Nonwovens applications such as medical, hygiene and cosmetics demand two non-negotiable rules: zero-tolerance and reliability. Contamination control is the supreme discipline in producing nonwovens for sensitive applications. The Uster contamination sorter masters this essential job with ease and security. It ensures customer satisfaction and a perfect experience for the final consumer – whether the end-product is made of natural or synthetic fibers.
Natural and pure
Bio-cotton is a trend growing from the sustainability movement. Customers are willing to pay higher prices for ‘all natural’ products. It’s a promising business scenario, but a tricky one! Bales of cotton typically contain various kinds of contamination – none of which should get into the final product, and ideally should be removed at the earliest stage of production.
Eliminating contamination during fiber preparation – and before the contaminants are shredded into smaller particles by the further processes – absolutely improves the quality of the raw material and reduces waste. The Uster Jossi Vision Shield N contamination sorter ensures the best possible detection and removal of contamination, right after the fiber opener.
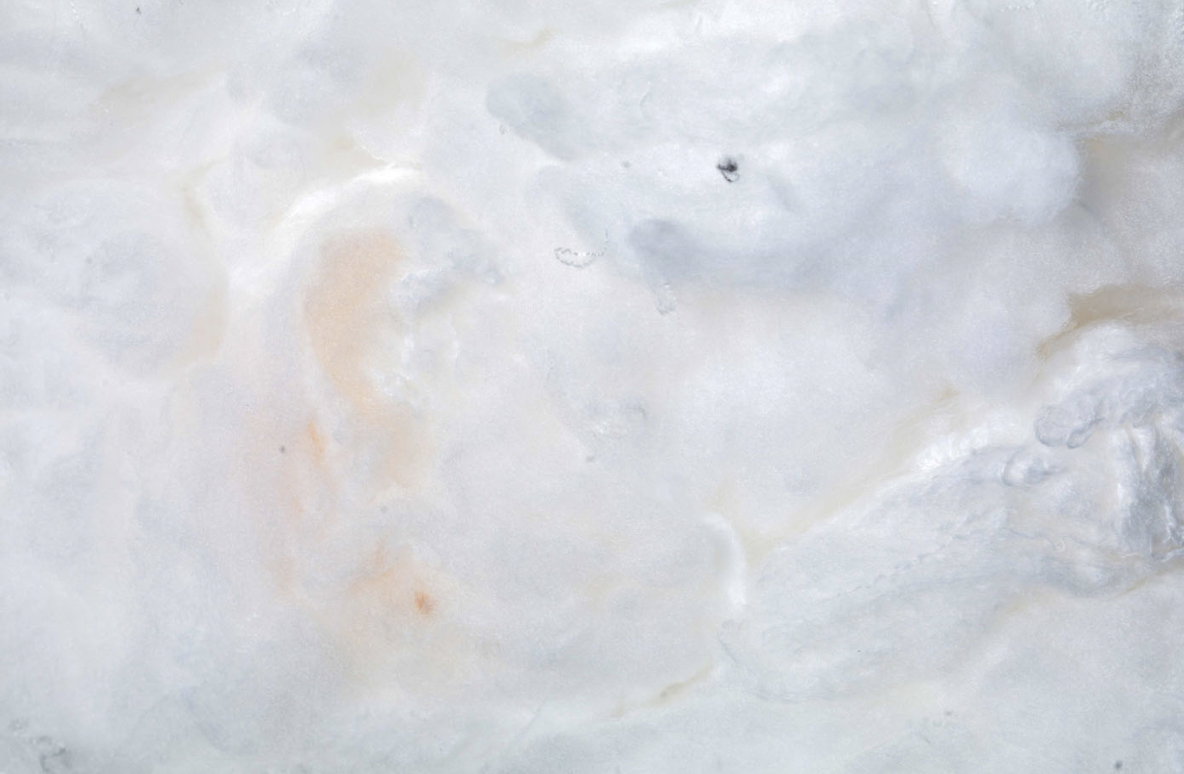
Conventional camera-based systems cannot match the performance of the top-level spectroscope technology from Uster. The high-end Imaging Spectroscopes in Jossi Vision Shield N are backed by over 20 years’ experience. These spectroscopes can find contamination even within the ‘invisible’ range of IR and UV light.
The same expertise also works with bleached cotton. Fragments of contamination in light pastel colors and white are also no problem. The ‘Quick Teach’ feature automatically learns the correct color of each new raw material, to prevent false ejections when material lots are changed.
Synthetic and clean
Nonwovens producers expect high quality and no contamination when purchasing synthetic fibers. Control is the only secure method when operating a business in highly sensitive applications such as medical textiles. Durable or non-durable, the product must be super clean. Contamination is not acceptable, and snow-white color generally a must. Producers have the security they need with Uster Jossi Vision Shield N. Detection of tiniest contamination fragments, even in light pastel colors and whites is not a problem.
Slim and powerful
Uster Jossi Vision Shield N is the result of surveys, close collaboration with international nonwovens companies and countless hours of field tests. Installation is easy, since the fiber cleaner’s slim design fits perfectly into existing lines. The system readily copes with the pace of standard production environments – up to a capacity of 2,000 kg per hour. Stainless steel inserts, in areas which come into contact with the fibers, guarantee unmatched durability.
The future-oriented graphical user interface gives a quick overview of running performance in real time, on a large high-resolution touchscreen, showing the most relevant data at a glance. User- friendly, quick and intuitive navigation makes data handling easy.
No fault, no risk
Managing quality with Uster Jossi Vision Shield N at the fiber preparation stage gives manufacturers the total confidence that only contamination-controlled products are delivered. The paramount need is to prevent defects from the production processes reaching the end-product – and the Uster system simply does that.
Uster Technologies has built experience and technological know-how over nearly three decades of fiber cleaning in spinning. Contamination is unwelcome in yarn, just as it is in nonwovens! Worldwide, 5,000 installations of Jossi Vision Shield fiber cleaning systems in spinning mills underline Uster’s success.